Known for its distinctive appearance, Finetrack’s Elemental Layer has earned nicknames like 'fishnet' or 'see-through layer.' The fabric’s unique design, characterized by countless mesh openings, immediately captures attention.
These mesh openings function as 'sweat pathways,' effectively allowing moisture and precipitation to escape naturally during outdoor activities. This innovative feature plays a vital role in Finetrack's dry layering concept, designed to keep your skin comfortably dry in challenging conditions.
In the first installment of the series 'The Story of Elemental Layer,' we explore the fascinating origins of these mesh openings. What secrets and innovations lie behind their creation?
Rows of neatly arranged openings, just a few millimeters apart—upon closer inspection, you can see that they go all the way through.
This is called a perforated mesh. In typical circular-knit fabrics, it’s common for several threads to run across the openings. However, in Elemental Layer, there are no threads crossing these openings—they are completely perforated. This unique design is exceptionally rare and represents a complex achievement in fabric construction.
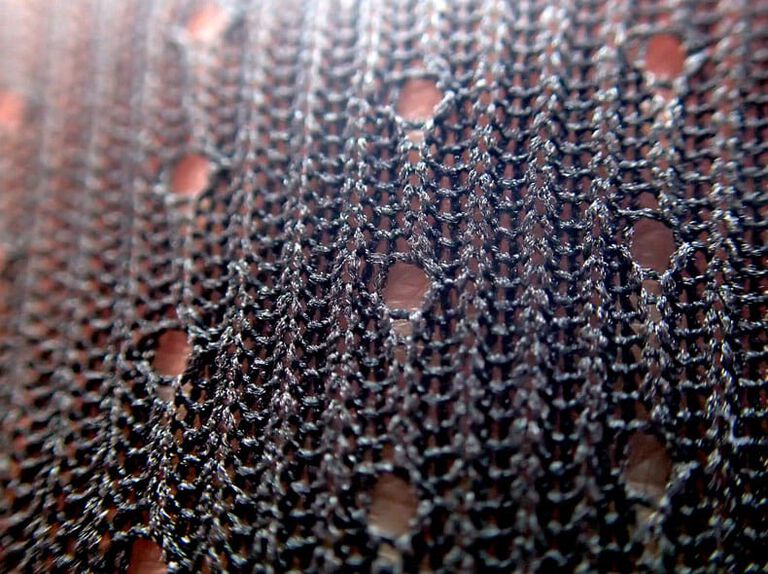
These perforated mesh openings serve two purposes: to let sweat pass through and to increase opportunities for the fibers of the base layer worn on top to make contact with the moisture and wick it away.
'To ensure sweat could escape freely, it absolutely had to be perforated,' explains Yotaro Kanayama, the developer and founder of Finetrack.
This perforated mesh is created using the circular knitting low-gauge technique that was widely used around the 1960s. If you remember traditional undergarments with patterns of diamonds or flowers formed by dotted holes, this may ring a bell.
Today, this technique has almost disappeared, and even manufacturers of the machines required to produce it no longer exist. It’s somewhat surprising that this old-fashioned method is now being applied to cutting-edge mountaineering underwear.
When development began, some were skeptical, wondering, 'Why use such an outdated technique?' But it was all for the purpose of creating a 'sweat pathway.'
The mesh fabric was developed in collaboration with Unichika Trading, headquartered in Osaka. Jun Tanaka, a sales representative responsible for Finetrack, recalls the development process from 14 years ago:
'Typically, fabric development begins with a sample—a starting point to discuss and refine, such as "something like this, but with a different type of knit." However, Finetrack approached the development of Elemental Layer without any existing samples. The process began entirely from scratch, requiring countless meetings to align ideas and determine how to turn the concept into reality.'
As one of Japan's leading synthetic fiber manufacturers with a network of knitting factories, Unichika Trading was an ideal partner for the project. Tanaka, specializing in sports knit development, played a pivotal role in bringing Elemental Layer to fruition.
'In pursuit of better sweat permeability, we ended up with this old technique. Coincidentally, one of the knitting factories we worked with still had the old machinery capable of creating perforated mesh,' Tanaka explains.
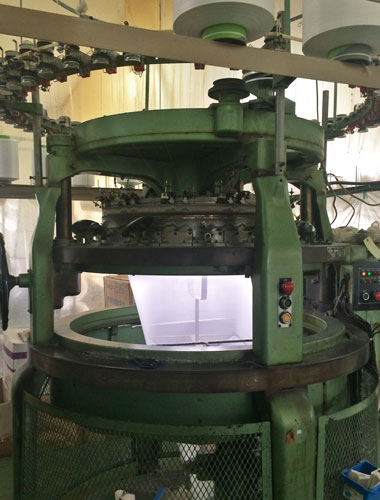
Knitting this ultra-thin perforated mesh fabric with modern machines is nearly impossible due to its complexity.
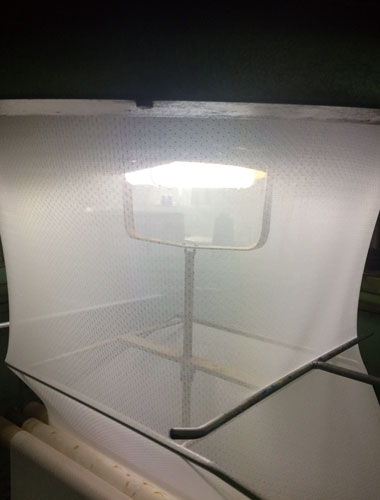
At times, dormant machines were revived from the warehouse, enabling us to ramp up production.
We searched for machines that had become almost like antiques, brought them out, performed maintenance, and test fabric was woven. When the fabric arrived, we made prototypes, tested them by wearing them in the mountains, and gave feedback. The search for the 'path of sweat'—such as hole size, pitch, and fabric thickness—became a year-long process of trial and error in a partnership between two people.
Amidst the trial and error, what Finetrack focused on most was real-world testing in the mountains. When creating something that doesn’t exist in the world, there are no reference values or testing methods. The painstaking process of testing it ourselves and observing how it performs in the mountains was seen as the most important aspect.
Mr. Tanaka shared an interesting story: "As a fabric supplier, the R&D team wanted to scientifically prove that sweat could escape, so they conducted tests in the lab using fabric samples... but the results weren’t successful. Concerned, I spoke to Mr. Kanayama, and he said, 'When you wear it as a shirt, it properly lets sweat escape. Don’t worry!' and wasn’t concerned at all."
The combination of old and new Japanese technology, coupled with the practical expertise of mountaineers, ultimately led to the creation of the original textile with its distinctive mesh openings that effectively let sweat pass through.
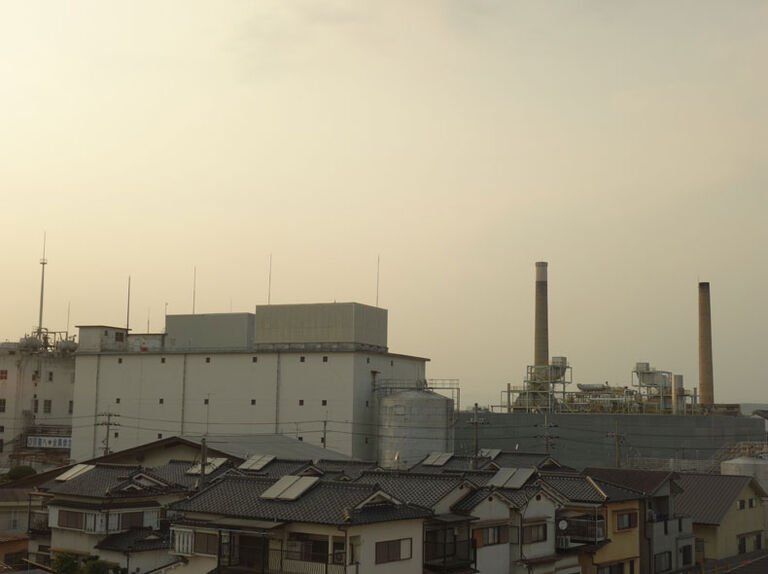